The Product as a Service (PaaS) model is revolutionising traditional manufacturing by shifting the focus from selling physical goods to offering products as part of an integrated service. This approach aligns with the growing trends of sustainability, circular economy, and digital transformation, enabling businesses to create new revenue streams, reduce waste, and enhance customer satisfaction.
What is Product as a Service (PaaS)?
The PaaS model involves manufacturers retaining ownership of their products while offering customers the benefits of usage, maintenance, and upgrades. Customers pay for the utility or outcomes provided by the product rather than owning it outright.
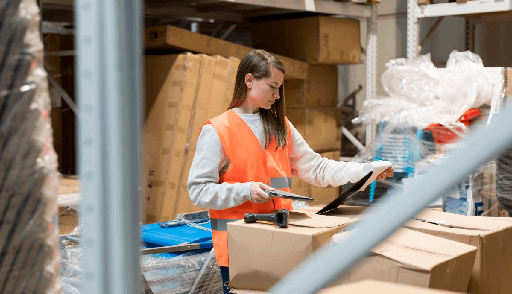
Examples:
- Automotive: Subscription-based car ownership like Volvo’s Care by Volvo.
- Technology: HP’s managed print services, where customers pay per page printed.
- Industrial Equipment: Caterpillar offering machinery leasing with predictive maintenance as part of the package
Key Features of PaaS Models
- Usage-Based Billing: Customers pay based on usage (e.g., hours of machine operation or energy consumption).
- Enhanced Maintenance and Support: Manufacturers provide ongoing maintenance, ensuring optimal performance and product longevity.
- Product Ownership: Companies retain ownership of the product, enabling easier recycling or repurposing.
- Flexibility for Customers: Businesses can scale services up or down based on their needs without investing in upfront ownership costs.How PaaS Benefits the Manufacturing Industry
Benefits of PaaS Model
1. Revenue Generation and Customer Retention
- PaaS creates a steady stream of recurring revenue
- Builds long-term customer relationships through continuous service rather than one-time sales
2. Sustainability and Circular Economy
- Manufacturers maintain responsibility for product lifecycle and end-of-life disposal
- Reduces waste by encouraging repair, upgrade, and reuse
3. Enhanced Efficiency
- Predictive analytics and IoT enable effective upkeep and maintenance
- Minimizes downtime through real-time monitoring and proactive service
4. Cost Savings for Customers
- Removes the barrier of upfront costs, making advanced equipment more accessible
- Predictable operational expenses through service-based payments
5. Data-Driven Insights
- IoT sensors and AI provide valuable data on how products are used, helping manufacturers improve design, efficiency, and customer satisfaction
Technology Enablers of PaaS
- IoT and Telematics: Enables real-time monitoring of product performance, tracks usage patterns to aid equipment servicing and plan proactive maintenance
- Artificial Intelligence (AI): Predicts when maintenance is needed, reducing downtime. Helps design more efficient products by analyzing customer usage data
- Blockchain Technology: Ensures transparent and secure transactions, tracks product lifecycle, and maintains service records
- Cloud Computing: Enables real-time data processing and storage, facilitating communication between manufacturers and customers
- Digital Platforms: Centralized platforms enable customers to subscribe, manage, and track their services. Example: GE's Industrial Internet platform for equipment management
Challenges in Implementing PaaS Models
- Initial Investment: Significant upfront costs for IoT devices, data analytics systems, and customer service infrastructure.
- Cultural Shift: Transitioning from product sales to service-based relationships requires mindset and operational changes.
- Customer Trust: Confidence in the hardware's usage PaaS model is still in a state of being constructed.
- Regulatory and Legal Barriers: Issues around ownership, liability, and data privacy need clear frameworks.
- Maintenance and Lifecycle Management: Manufacturers must invest in robust systems to handle repair, reporting, and upgrades efficiently.
Future of PaaS in Manufacturing
The PaaS model is expected to grow significantly as industries adopt smart manufacturing and embrace sustainable practices. Emerging trends include:
- AI-Driven Service Personalization: Tailoring services to individual customer needs using AI insights.
- Advanced Predictive Maintenance: Using machine learning and IoT data to predict and prevent equipment breakdowns.
- Decentralized Platforms/Leveraging blockchain for secure and transparent PaaS transactions.
- Collaboration/Ecosystems/Partnerships with third-party providers to deliver comprehensive service models.